Standard Reference Gases: Manometric Calibrations of CO2
A High Precision Manometric Analysis System to Define the WMO Mole Fraction Scale for CO2 in Dry Air
Introduction
A better understanding of the global carbon cycle is central to resolving uncertainties surrounding the future rate of global change. A major tool in the study of the carbon cycle is provided by the detailed temporal and large-scale spatial patterns of the mixing ratio of CO2 in the atmosphere. A fundamental requirement is careful and continuing calibration for CO2. Without a solid and precise link to a common calibration scale, many of the global measurements would be useless in meeting the goals of the carbon budget study.
Measurements of atmospheric CO2 are made using laser spectroscopy or nondispersive infrared (NDIR) analyzers. These techniques require accurately calibrated reference gases. We use the manometric method to determined the absolute mole fraction of CO2 in a series of 19 primary standard. Primary standards are analyzed by manometry every 2-3 years to build up a history of measurements and track possible changes over time. GML has been designated as the Central Calibration Laboratory (CCL) by the WMO to help determine the international scale against which CO2 measurements are reported.
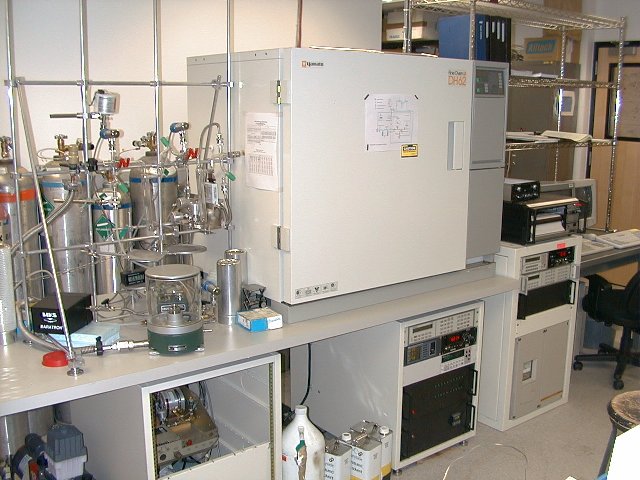
Manometric Apparatus
A manometric apparatus that can be easily and repeatedly employed to perform calibrations has been developed by the CCGG group. This system is illustrated in Figure 2.
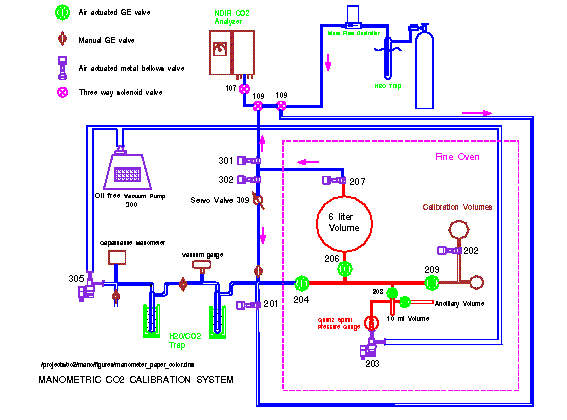
The apparatus is principally made of glass. It consists essentially of a 6-L Pyrex glass flask connected by means of a manifold to a 10-mL Pyrex glass volume. A high-quality pressure gauge is used to measure the pressure in the 6-L and 10-mL volumes. Two additional intermediate size glass flasks are used for calibrations of the volume ratio of the 10-mL and the 6-L volumes. Pressure and temperature are traceable to nationally-recognized standards and to the SI. All of the components are enclosed in an oven, where the temperature is regulated to an accuray of 0.01° C. (Figure 3).
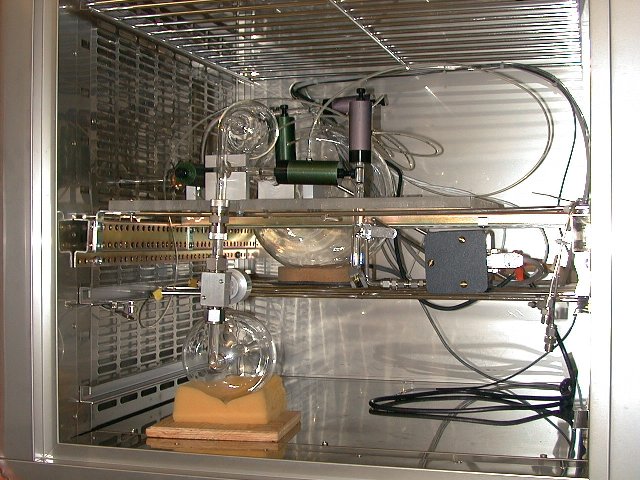
Two liquid nitrogen cold traps connected to the manifold are used for CO2 collection when the sample gas is extracted from the large volume.
Principle of measurement method
To begin the manometric calibrating process, the glass manometric chamber including the 6-L large volume are evacuated to a residual pressure of less than 5 mtorr. Sample air from a cylinder to be analyzed is passed through a 1 m long, 3 mm diameter copper coil immersed in an alcohol bath at -65 to -70°C to remove water vapor. The gas then flows into the evacuated glass volume until the pressure in the volume reaches 83kPa. The gas is then allowed to come to equilibrium, and the temperature and pressure are measured. The sample air is then slowly pumped out through two liquid nitrogen traps, freezing out CO2, N2O and residual water vapor. The pressure of the gas entering the traps is maintained at 0.4 kPa (~ 3 torr). This step takes about 40 minutes. The frozen CO2 and N2O in the traps is distilled several times to remove water vapor by surrounding the traps with a dry ice-alcohol mixture. The CO2 and N2O are then transferred to the 10-mL volume by placing liquid nitrogen around the small volume and removing the dry ice-alcohol mixture from the traps. The trapped CO2 and N2O are then thawed and the pressure and temperature are continuously measured while equilibrium is reached. This takes about one hour. The molar ratio of the CO2 in the original air sample can be calculated with the virial equation of state, using a predetermined ratio of the large to small volumes, and taking real gas compressibility into account.
Results
Since the first manometric calibrations in 1996, when the reproducibility of the manometric analyses was 0.12 ppm, it has gradually improved to about 0.07 ppm in 2015.
References
The manometric calibration system is described in more detail in:
- Zhao, C. L. and P. P. Tans (2006), Estimating uncertainty of the WMO mole fraction scale for carbon dioxide in air, Journal of Geophysical Research-Atmospheres, 111(D8), 10.1029/2005JD006003.
- Zhao, C., P.P. Tans and K.W. Thoning, A high precision manometric system for absolute calibrations of CO2 in dry air. Journal of Geophysical Research102(D5):5885-5894 March 20, 1997